首檢控制在實際操作中的要點,首檢控制在生產實踐中的關鍵操作要點解析
首檢控制在生產制造過程中是確保產品質量的關鍵環節,其核心在于通過首次檢驗及時發現并糾正潛在問題,避免批量性缺陷,實際操作要點包括:1. **明確檢驗標準**,依據工藝文件、圖紙或客戶要求制定清晰的首檢項目與合格范圍;2. **規范操作流程**,首檢需在生產初始階段由專人完成,覆蓋設備參數、原材料、首件成品等全要素;3. **記錄與標識管理**,詳細記錄檢測數據并對首檢樣品進行標識隔離,便于追溯;4. **異常處理機制**,若首檢不合格需立即停機分析原因,調整后重新檢驗直至達標;5. **責任落實**,操作者、質檢員需共同確認結果,避免疏漏,首檢應結合過程巡檢形成閉環控制,尤其適用于換模、換線或工藝變更后的生產啟動階段,以降低質量風險,提升效率。
一、首件定義相關要點
- 明確首件的界定條件
- 在生產過程中,每個班次剛開始時,或在過程發生改變(如人員變動、換料、換模具、設備修理、工藝變更、工裝刀具的調換修磨等)后加工的第一或前幾件產品為需要進行首檢的首件產品。例如在汽車零部件生產企業、電子制造企業等制造業場景下,這些情況發生時所產生的相關產品均需首檢。
二、檢驗前的準備要點
- 制度與標準方面
- 建立明確制度規范:要有明確的首件檢驗管理制度/程序,明確首件檢驗的范圍和要求。例如規定哪些工序、哪些類型的產品變更時需要進行首檢等內容。
- 明確檢驗標準:分工序為需要進行首件檢驗的產品制定檢驗標準,包括檢驗項目、檢驗方法、樣品數量、判定依據等。這確保檢驗人員在操作時有據可依,能準確判斷首件是否合格。
- 人員與工具配備
- 人員培訓:確保操作人員、班組長、檢驗員等相關人員熟悉首檢流程、標準以及各自的職責。例如操作人員要知道如何進行自檢,檢驗員要清楚專檢的具體要求等。
- 工具配備:為每一個需要首件檢驗的工序/崗位/機臺配備符合產品測量要求的檢驗工具,如測量尺寸的量具等,以便能準確進行檢驗操作。
三、檢驗過程中的要點
- 檢驗項目涵蓋范圍
- 基本信息核對:檢驗圖號與工作單是否符合;材料、毛坯或半成品和工作任務單是否相符;材料、毛坯的表面處理、安裝定位是否相符;配方配料是否符合規定要求等。這能確保生產源頭的正確性。
- 質量特征檢驗:檢驗首件產品加工出來后的實際質量特征是否符合圖紙或技術文件所規定的要求,如尺寸、外觀、性能等。例如機械加工零件的尺寸精度、電子產品的功能性能等方面的檢驗。
- 采用三檢制:自檢、互檢及專檢。送檢的產品必須先由操作人員進行“自檢”,然后再由班組長或同事進行“互檢”,最后由檢驗員“專檢”,確定合格后方可繼續加工后續產品。只有經過這三道檢驗關卡,才能最大程度確保首件的質量。
- 檢驗數量要求
- 一般要檢驗連續生產的3 - 5件產品,合格后方可繼續加工生產。不同企業或客戶可能會根據實際情況對檢驗數量有具體的要求,但通常在這個范圍內確保能有效發現潛在問題。
四、檢驗后的要點
- 結果標識與記錄
- 首件標識:檢驗員對檢驗合格的首件產品,應打上規定的標記,并保持到本班或一批產品加工完了為止(所有首件產品必須留樣,留作后續產品對比之用,并用記號筆標記“√”以示通過首件檢驗)。這有助于在生產過程中隨時進行對比參考,監控生產過程是否穩定。
- 認真記錄:要設計并使用檢驗記錄,并在生產現場/崗位/機臺使用,明確記錄的填寫要求。詳細記錄首件檢驗的相關信息,如檢驗時間、檢驗人員、檢驗結果、問題發現與處理等情況,以便后續查詢和追溯。
- 問題處理與反饋
- 不合格處理:首件檢驗不合格,需查明原因、采取措施,排除故障后重新進行加工、進行三檢,直到合格后才可以定為首件。例如如果是設備故障導致首件不合格,要先修復設備再重新生產和檢驗首件。
- 反饋改進:通過分析首件產品的問題和缺陷,企業可以找出生產過程中的薄弱環節和潛在問題,從而制定針對性的改進措施,反饋到生產流程中,促進持續改進。
- 動態更新:檢驗標準和記錄不是一成不變,應隨著質量水平的提升或新的質量問題的出現,進行動態調整更新。確保首檢控制能適應生產過程中的各種變化,始終保持有效性。
- 檢查驗證:質量管理或檢驗技術人員,應經常深入生產一線檢查首件工作執行情況,及時發現問題,確保有效落實。這有助于保證首檢制度在實際操作中不被忽視或流于形式。
首檢控制常見問題及解決方案
首件檢驗與后續產品質量關系
如何提高首件檢驗效率
首檢控制在不同行業應用案例
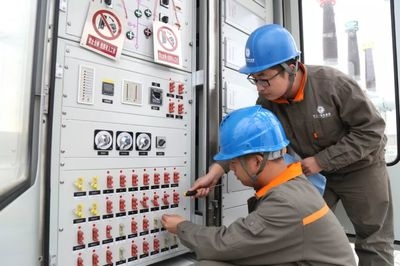
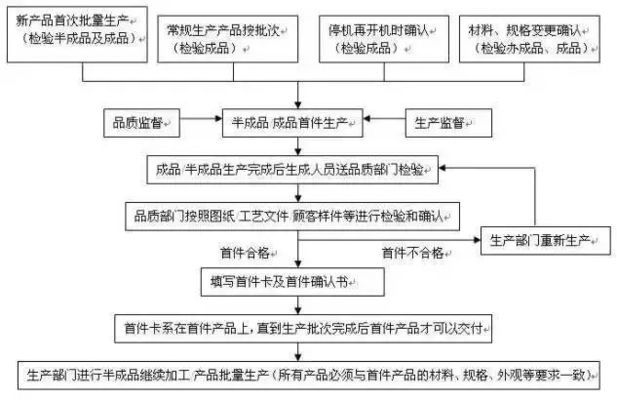
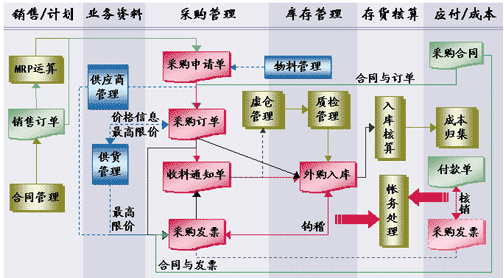

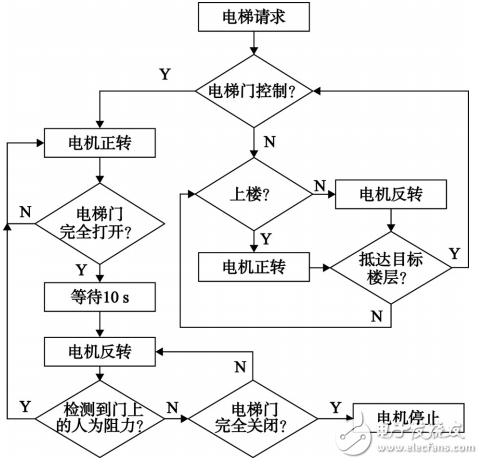
文章版權聲明:本站文章基本來源于網絡,如有不妥請聯系店長刪除
發表評論
還沒有評論,來說兩句吧...